コロナ禍にDIYで作成した在宅勤務用の机が手狭になってきました。そこで今回は、”カフェ板”と2×4材を使用して新たな机を作成していきます。複数のカフェ板をダボ継して1枚の天板にする方法や、2×4材での机の土台部分を作成する方法、ニスで天板表面を仕上げる方法などを紹介します。下記リンクにて動画も公開していますので、皆さんのDIYのご参考にしてみてください。
1.手狭になってきた在宅勤務用の机
私は現在、有難いことにほぼ毎日、在宅でお仕事しています。
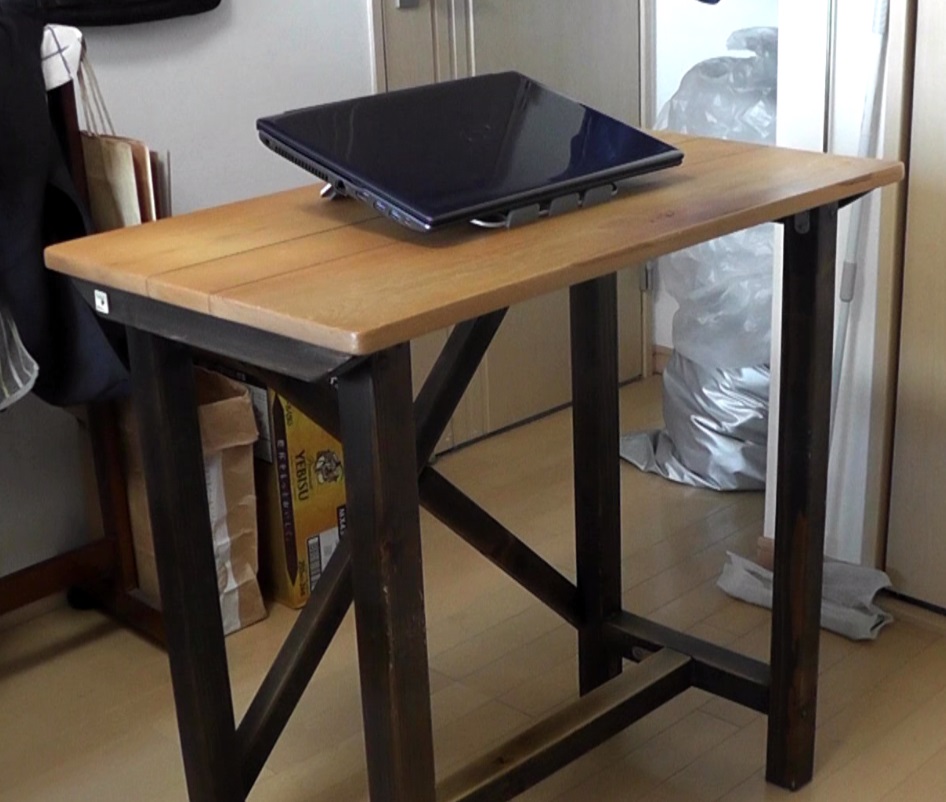
お仕事用の机は、以前にDIYで作成した、1×4材と1×6材2枚を繋ぎ合わせた天板の写真の机です。
天板のサイズが「450mm×785mm」と小さいので、B5サイズ(257mm×364mm)のパソコンを使用すると作業スペースが足りません。
また、机の脚には、45mm×45mmの主に根太などに使用される角材を使用しましたが、机の高さに対してはかなり細い材料になるので、使用時のぐらつきを抑えるのに苦労しました。(背面側の筋交いで、何とかぐらつきを抑えています)
コロナ禍に在宅勤務が始まった時にDIYした机ですので、使用期間は賞味4年程度です。まだまだ問題なく使用できる机ですが、そろそろもう少し作業スペースが大きく安定性の高い机に変えていくことにしました。(4年間、お疲れさまでした)
2.繋ぎ合わせて使用出来るカフェ板とは?
作業スペースの大きな机を作成するためには、より大きな天板を作成する必要があります。天板の材料として、前々から気になっていたのは「カフェ板」です。
カフェ板は、よく乾燥させた杉の無垢材です。以前のDIYでは、廊下の本棚の上に設置した棚や、ベッドサイドに設置した棚の棚板にも使用した材料です。(詳細は、下記の過去記事をご参照ください)
最近では、取り扱っているホームセンターも増えていますので、大型のホームセンターに行けば大体購入できるはずです。
店頭で売られているカフェ板の主なサイズは、厚みが30mm、幅が200mm、長さは1m(1,000mm)、もしくは2m(2,000mm)です。(大型店舗には4mのものもあります)
価格は、私がお世話になっているスーパービバホームさんで、2mのものが¥1,150/枚でした。(2024年12月時点の価格になります。)価格的にもそれほど高価な材料ではないので、我々DIY師が手を出しやすい材料ですね。
また、カフェ板は、自然乾燥ではなく機械でしっかり乾燥させた材料になるので、購入後の変形などが少ないと言われています。そういった点でもおススメの材料です。(とはいえ、自然の材料なので、経験則的には多少の変形は発生しますけど。)
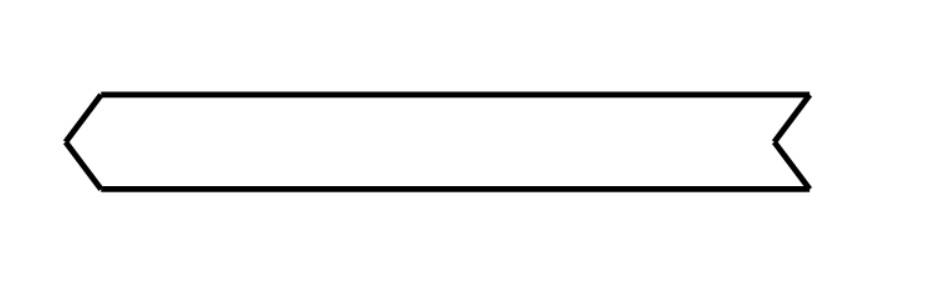
そして、短手方向の断面形状が図のようになっていますので、端面の凹側と凸側を嵌めて使用することで、板どうしを隙間なく並べることが出来ます。(上から見た時の隙間が発生しません。)そのため、複数枚をつなぎ合わせて机の天板や棚板として使用されたり、洋室の床板などに使用されたりする材料になります。(床板が厚みのある杉の無垢材なんて素敵ですよね!)
ただし、カフェ板には「節」の穴が開いているものが多々あるので、天板や床板に使用する場合には、節目をパテで埋めるなどの処理が必要になりますので、その点は注意が必要ですね。
今回は、そんなカフェ板を繋いで天板にして、新たな机をDIYしていきます。
3.DIYで作成する机を設計する
新たに作成する机の天板には、カフェ板を使用することにしましたが、その前提条件をベースに、机全体を設計していきます。

まず、机の脚となる材料には、流通性が良く安価な2×4材(写真)を使用します。
現状の机は、脚に45mm×45mmの角材を使用しているので床との接地面が小さいですが、2×4材の断面は38mm×89mmです。床と接地する面積を1.67倍にすることが出来ますので、机の安定性を向上させることができるはずです。
また、現状の机では使用時のぐらつきを抑えるのに苦労しましたので、今回はその辺りも考慮して、机の脚どうしをしっかり連結させて、ぐらつきの少ない構造にしていきます。
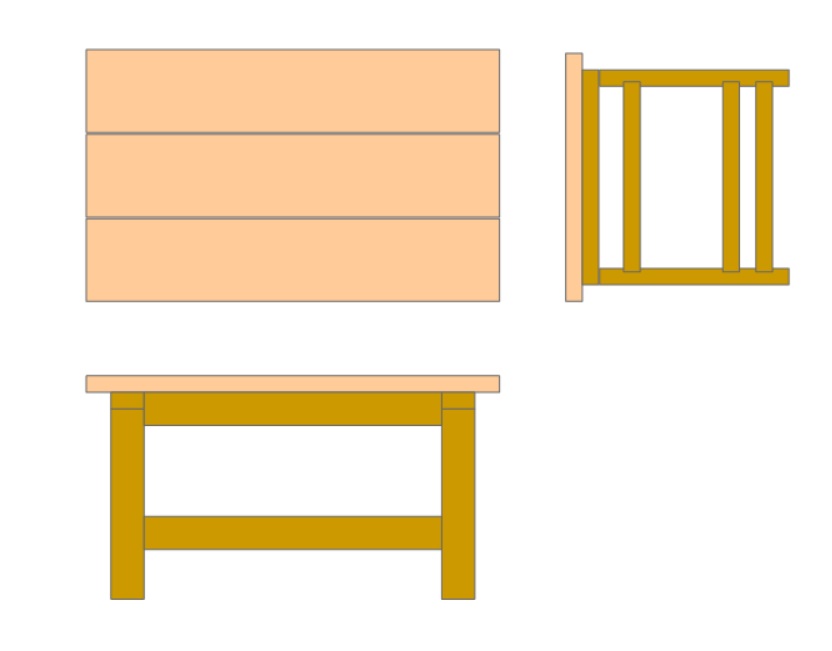
その辺りを踏まえて色々と検討した結果、今回作成する机の基本構造は図のとおりとしました。
天板は3枚のカフェ板を繋ぎ合わせて作成します。
そして、2×4材で作成する脚は、左右の脚それぞれを、6本の2×4材で構成し、その左右の脚を3本(前1本、後ろ2本)の2×4材で連結して机の土台としていきます。
この構造であれば、机の左右に配置する脚はかなり強固になりますので、少なくとも前後方向の机のガタつきはかなり抑えられるでしょう。左右についても、2つの脚を3本の2×4材で連結することで、ガタつきはかなり抑えられると思いますが、それで足りないようであれば、更に2×4材を追加して対応していきます。
カフェ板の反り止めなどの詳細は、材料を購入しに行った時に改めて考えるとして、まずはこの設計で材料を購入して作成していきましょう!
4.カフェ板を繋ぎ合わせて天板を作成する
まずは、机の作業スペースとなる天板をカフェ板を繋ぎ合わせて作成していきます。
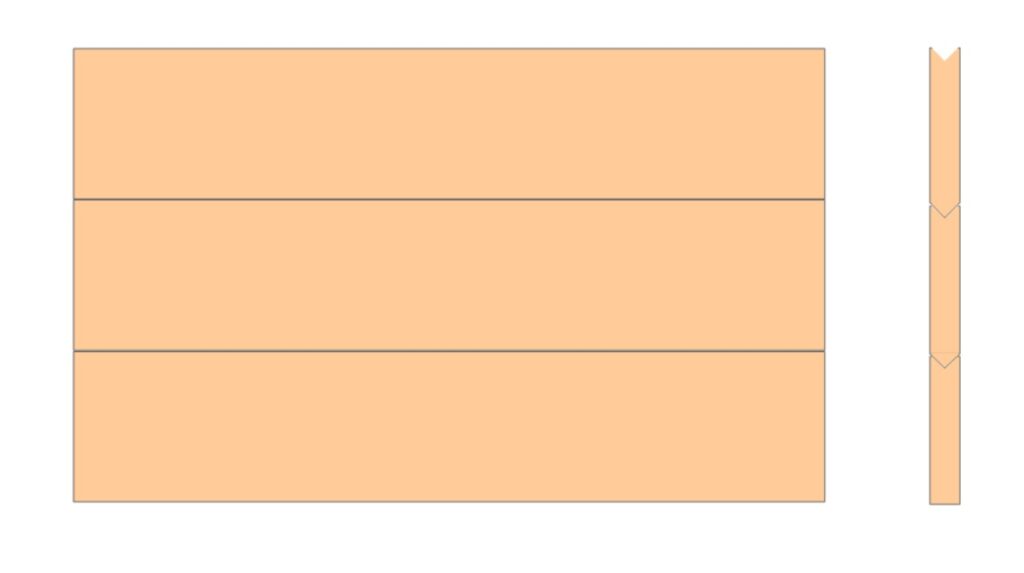
繋ぎ合わせるカフェ板は3枚です。横幅が1000m未満となる机を作成していきますので、今回は2mのカフェ板を2枚購入し、1m弱のカフェ板を3枚使用して、図のような天板を作成していきます。
また、机の前側となる端面は、凸部をカットして垂直に加工します。(奥側は基本的にブラインドとなるため、凹部の形状はそのままとします。)
なお、今回は出来るだけ節穴がないカフェ板を探して購入しましたので、木表側には全く節がない材料を購入することが出来ました。(木裏には多少の節穴があります。)天板作成後の反りを考慮すると、木表と木裏を互い違いにして繋ぎ合わせた方がよいみたいですが、今回は、3枚とも節穴がない木表側を表面にして繋ぎ合わせていきます。(木表の方がカンナを綺麗にかけられるというメリットもあります。)
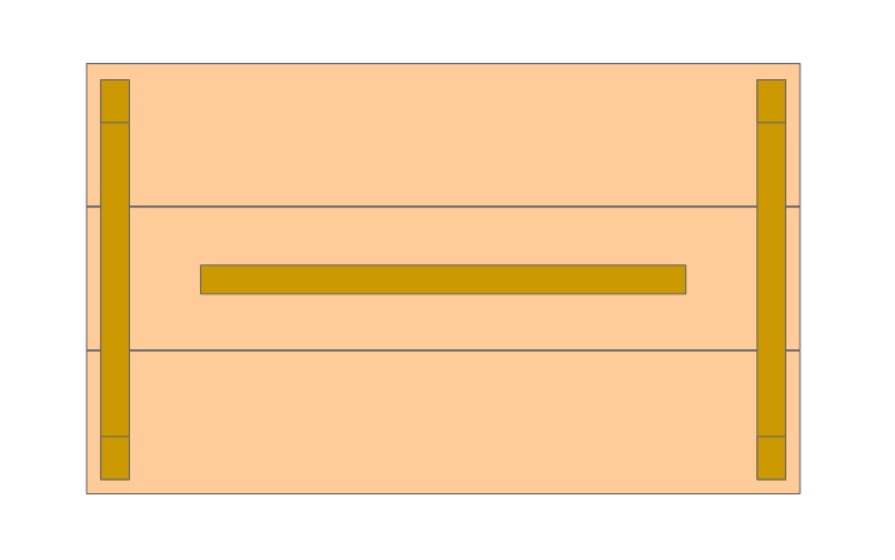
反り対策の材料には、35mm×45mmの角材を購入してきました。図のように天板の裏側に固定して反り止めとします。(脚の位置を避けて配置します)
ちょっと天板の反り対策が貧弱な気もしますが…まあ、脚が頑丈になるはずなので、脚としっかり連結させれば、何とかなるでしょうw
天板設計の詳細が決まったら、早速材料をカットしていきます。
まずは2mのカフェ板を、電動丸ノコで1mにざっくりカットしていきます。(カフェ板を繋ぎ合わせた後に両端を揃えてカットし直すので、この段階のカットはざっくりでOKです)
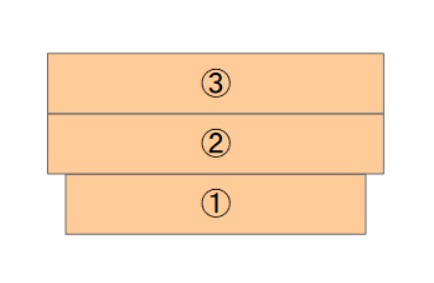
ただ、我が家には500mm程度のF型クランプしかないため、1枚200mm幅のカフェ板を3枚同時にクランプすることが出来ません。よって、図のように前側のカフェ板のみ少し短めにカットし、繋ぎ合わせる際には、先に①と②を繋ぎ合わせて、その後に①+②と③を繋ぎ合わせる順番で対応していきます。(①+②と③をクランプする際には、①と②の段差にクランプをひっかっけて③と圧着します)
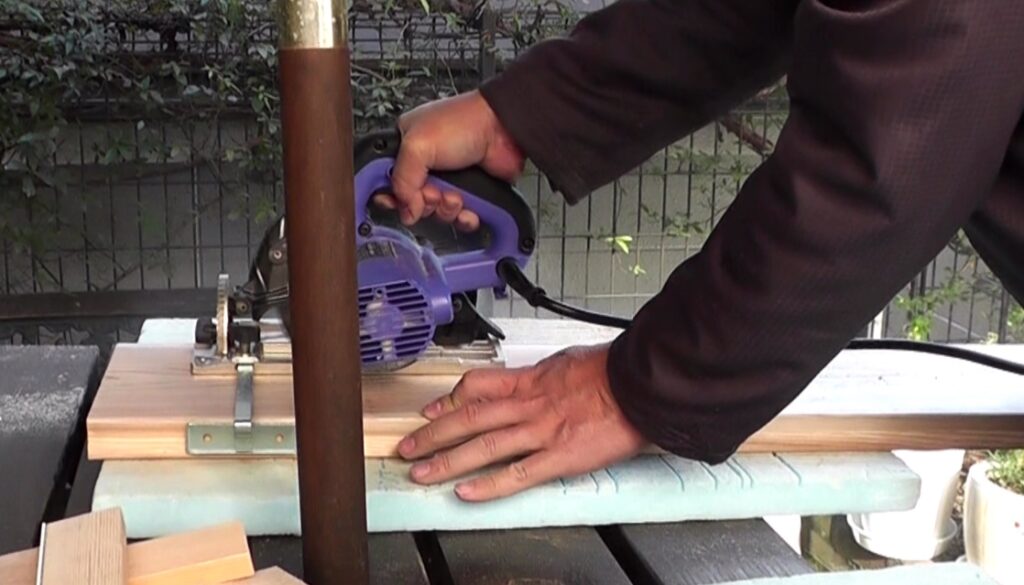
カフェ板の長手方向が想定の寸法でカットできたら、机の前面になる①の凸部(△の突起)をカットします。電動丸ノコで距離の長いカットをするのは少々苦手ですが、写真のように付属のガイドを使用すれば、それほどズレることなくカットできます。
材料がカットできたら、カフェ板どうしを繋ぎ合わせていきますが、今回繋ぎ合わせる方法は、Φ8mmのダボを使用した「ダボ継」です。ヒロミの八王子工務店などでは、ビスケットと呼ばれる円盤状のジョイントを使って繋いでいますが、あの工法は専用の道具が必要となりますので、我々DIY師はダボ継で十分だと思っています。(ホントはビスケットを使ってみたいですがw)
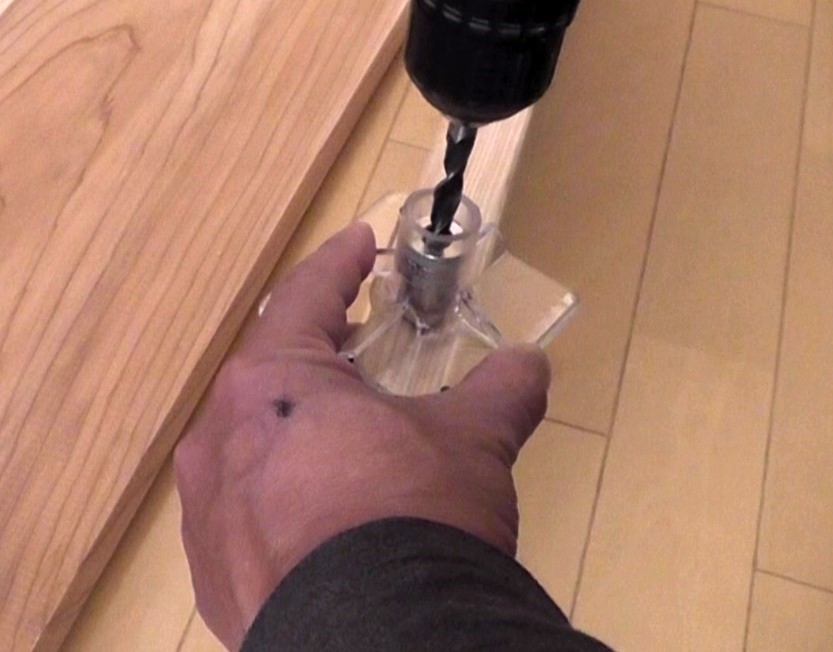
まずは、①の材料の②と繋ぎ合わせる面に、ドリルでΦ8mmの穴をあけていきます。材料に対して垂直な穴をあけることが重要になりますので、私は写真のようなドリルガイドを使用して穴あけしています。
また、今回は1つのつなぎ面に対して4本のダボを使用していきますので、カフェー板を繋ぐ面にバランス良く計4か所の穴を開けました。
①の材料に穴を開けたら、繋ぎ合わせる②の材料にも穴をあけていきますが、①と②の穴位置が正確に一致していないと、上手くつなぎ合わせることができません。
そこで私が使用しているのは、下記のようなダボ用マーカーです。
このマーカーをドリルで開けた①材料の穴に装着し、その状態でカフェ板どうしを合わせて、穴位置を②の材料に転写していきます。
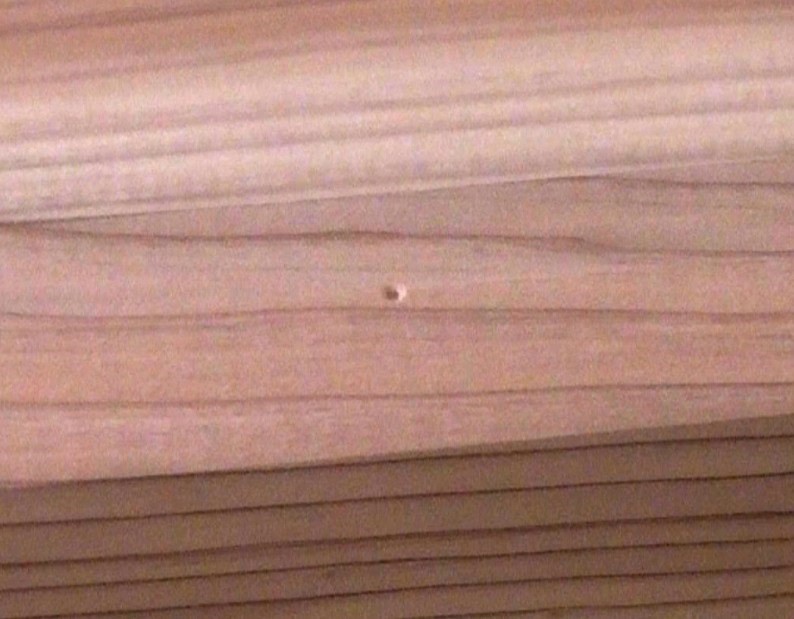
②の材料に転写したマーキングは写真の通りです。ここにドリルの先端を合わせて穴をあけることで、①材料と同じ位置に穴をあけることが出来ます。
①と②両方の材料に穴が開いたら、穴と合わせ面に木工用ボンドを塗布して、どちらかの穴にダボを挿入します。
そして、その状態で①と②を貼り合わせてF型クランプでしっかり固定したら、木工用ボンドが乾くまで圧着します。(一晩くらいは放置して完全硬化させます)
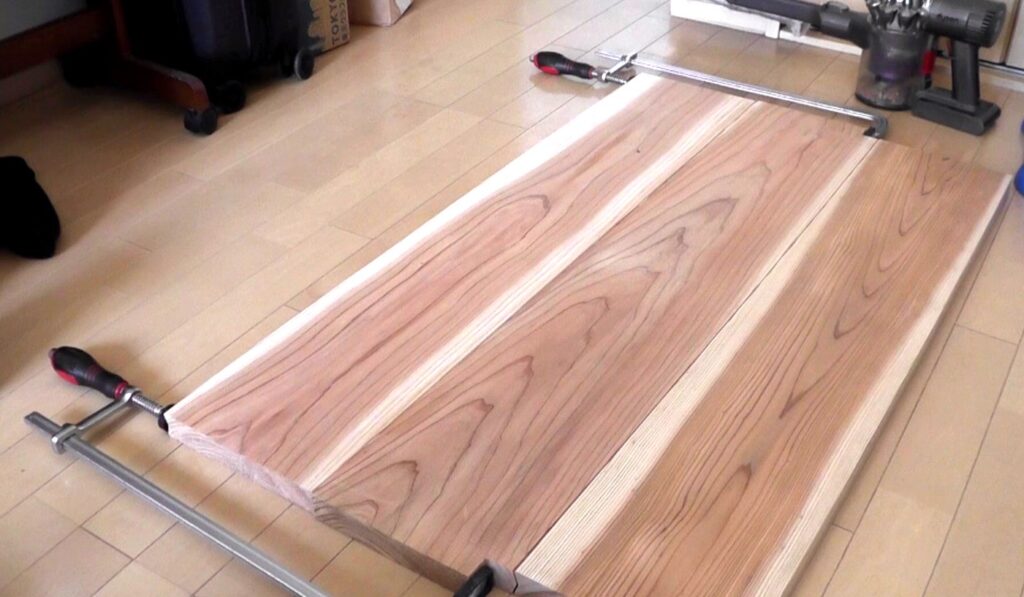
①と②を貼り合わせることができたら、次は①+②と③を繋ぎ合わせていきます。つなぎ合わせる工程は①と②を繋いだ時と同様です。②にドリルで穴をあけて③にその位置を転写し、③に穴を開けたらダボで繋いで圧着していきます。(写真のように①と②の段差を利用してF型クランプでクランプします)
この状態で木工用ボンドが完全硬化すれば、天板となる貼り合わせ材料は完成です。
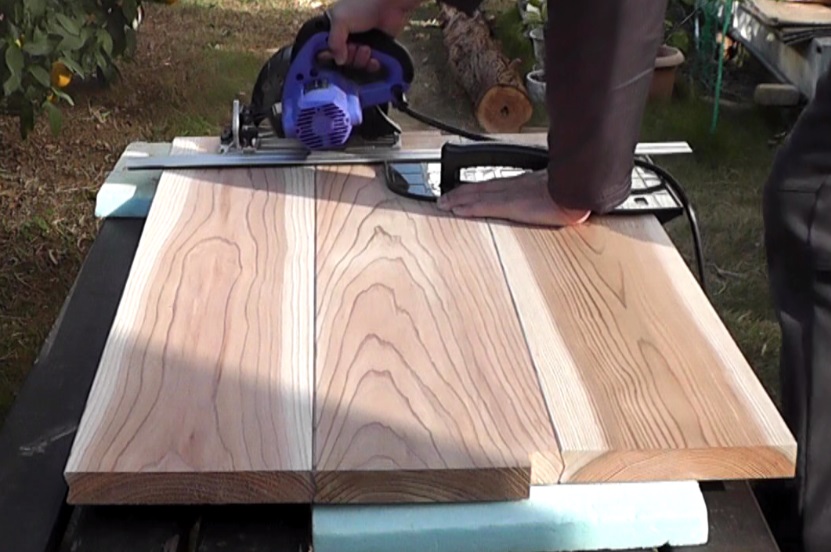
天板となる貼り合わせ材料が完全硬化したら、電動丸ノコを使用してその両端を切りそろえていきます。
なお、このカット面は天板の外観面となりますので、丸ノコガイドなどを使用して、材料に対してしっかり垂直にカットします。
両側を揃えてカットした結果、今回の天板の幅は940mmとなりました。(よって、今回作成する机の天板のサイズは、600mm×940mmです。)
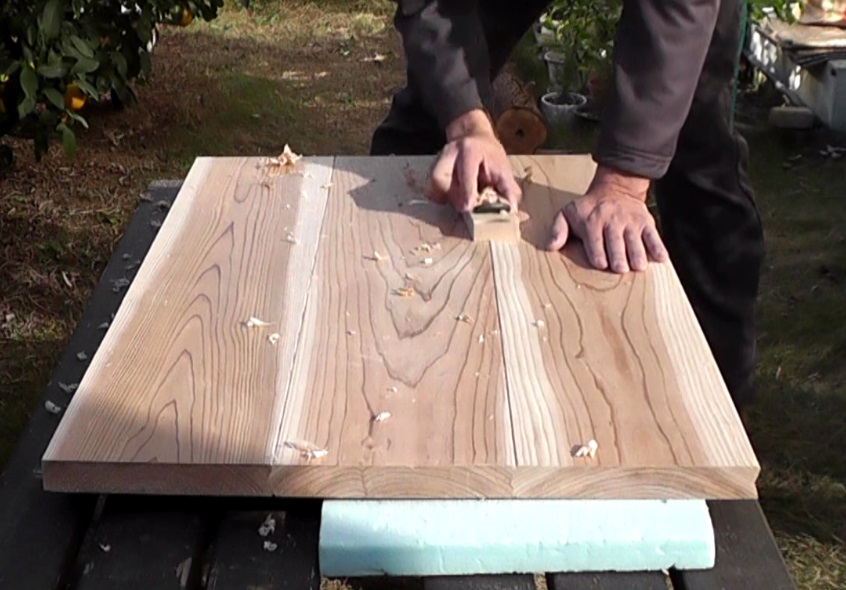
天板の両端がカットできたら、カフェ板どうしに出来た表面の段差をカンナで削って慣らしていきます。
以前はサンダーで段差を削っていましたが、広い面をサンダーで加工すると、硬い節の部分が削られずに残り、節部が少し膨らんだ状態になります。「平滑さ」を追求するのであれば、カンナを使用した方が良いです。
ただ、私のようなDIY初心者には、カンナは刃の突出量を調整するのがちょっと難しいですですよね?私の場合は、刃の突出量を最小限にして、薄く何回も削ることで対応しています。(急がば回れです)
なお、私が最近購入したカンナは下記です。耐久性の確認はこれからですが、角利産業さんのカンナは切れ味も良く、DIYであれば十分に使用できる良いカンナだと思います。
天板表面の段差が綺麗に処理出来たら、天板前面の角にRを付けていきます。
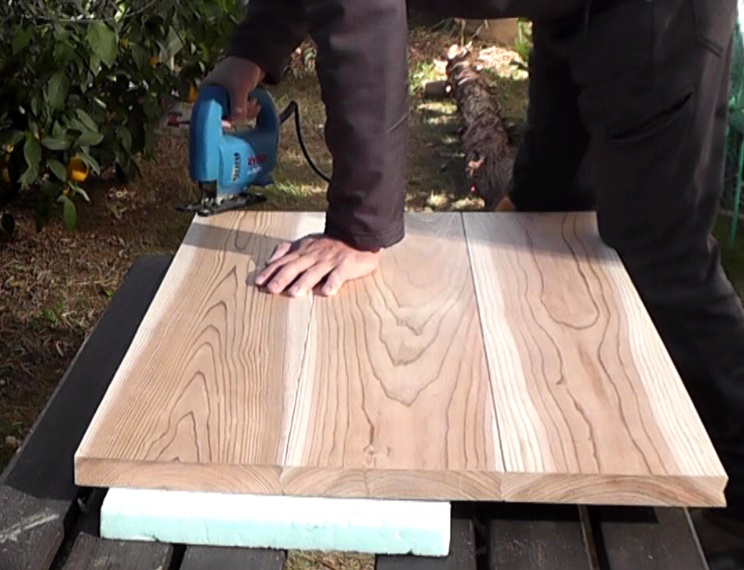
加工方法はディスクグラインダーで削るなど、色々な方法がありますが、今回は写真のジグソーで大まかな形状を加工して、サンダーで仕上げました。
なお、天板のリア面の角については、あまり触れる面ではないのでR加工は省略です。
天板前面のR加工が出来たら、天面のその他の角をカンナで削ってC面を付けていきます。
最後に全体をサンダー掛けしてツルツルに仕上げたら、天板の加工は完了です。
天板の加工が完了したら、続いては、反り止めとなる角材を裏面に固定していきます。
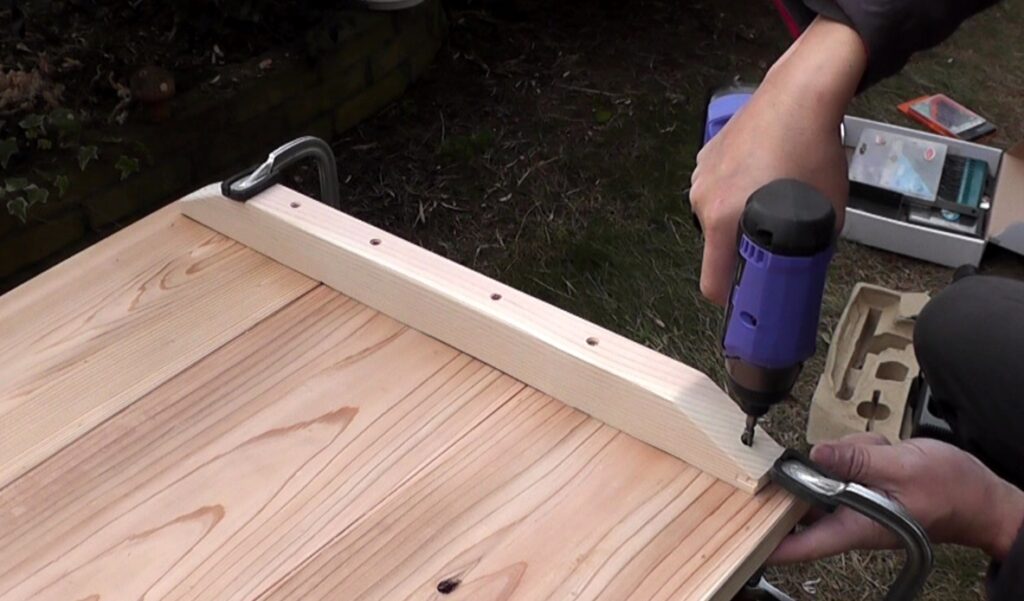
反り止めとして準備した35mm×45mmの角材を必要な形状に加工し、天板の裏面にネジ止めしていきます。
この際、ネジにコーススレッドを使用するなどして、材料どうしをしっかり密着させることが重要になりますが、F型クランプで固定してからネジ止めするとより確実に密着できますね。
また、この工程でネジの先が天板の表面にはみ出したら台無しです。ネジの長さや打ち込む深さはしっかり確認して加工しましょう。
ちなみに、私がネジを打つ深さを調整する際に使用している工具は下記です。
ドリルを使用するよりも、このような面取りカッターを使用した方が、穴の端面が綺麗に仕上がるのでおススメです。

反り止めの材料が全て固定出来たら、天板の加工は完了です。(写真参照)
うーん。やはり反り止め材が少々足りない気もしますが、頑丈な脚をしっかり固定して、その辺を補っていきましょう。
加工が完了したら、下記のオイルステインを塗布し、5分程乾燥させて余分なオイルを拭き取ります。それを更に一晩乾燥させれば天板の加工は完了です!
ちなみに、ステイン材は木目の生きるナチュラルがおススメです。(個人的な好みですが)
コメント